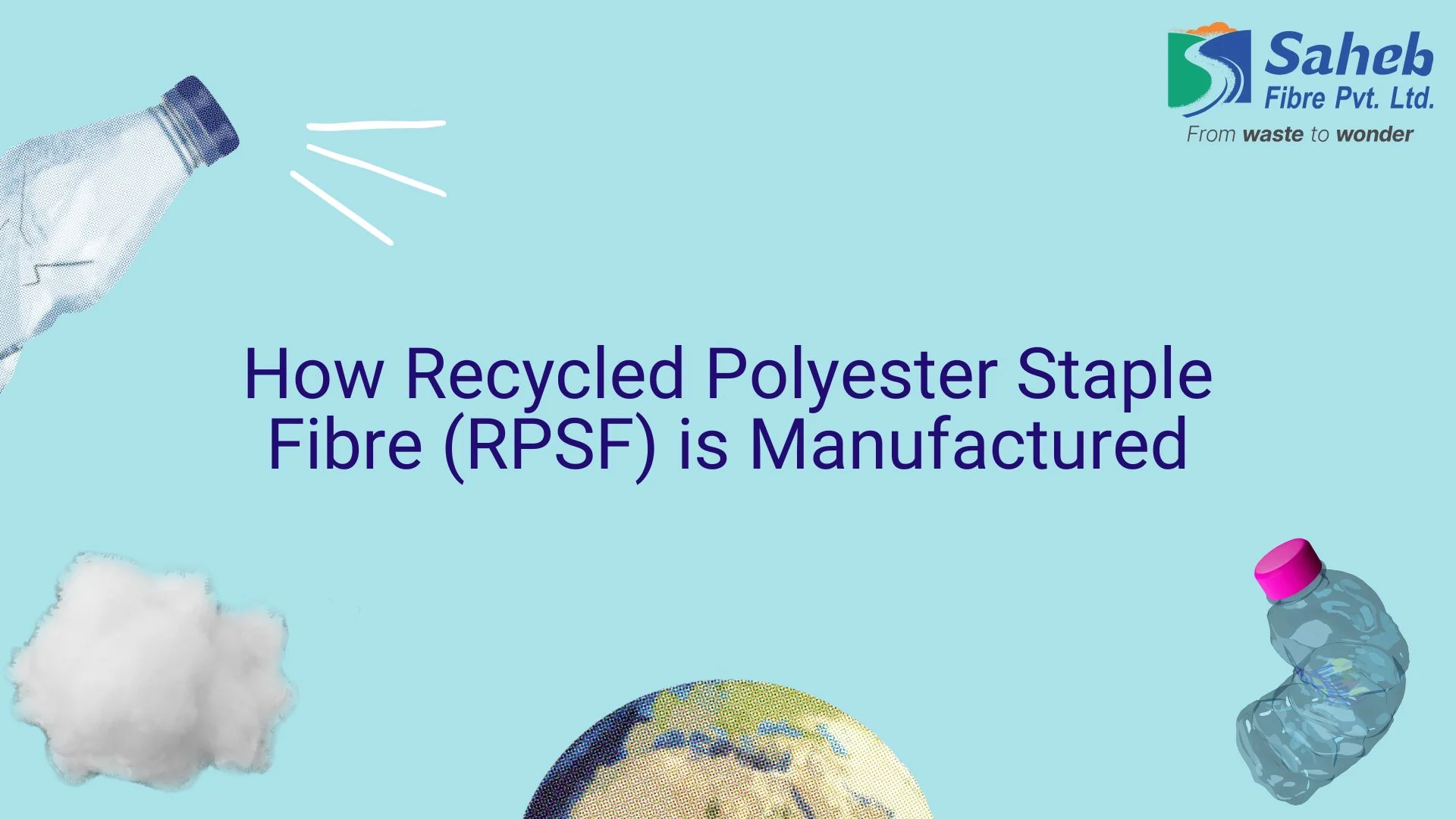
Recycled Polyester Staple Fibre (RPSF) is the principal product in sustainable manufacturing because of its critical role in waste reduction and enhancing circular economies. This article gives an in-depth overview of how RPSF is manufactured, the environmental impact of the manufacturing process, and what this means in relation to the modern textile industry.
Introduction to Recycled Polyester Staple Fibre (RPSF)
Recycled Polyester Staple Fibre or RPSF is a synthetic fibre derived from post-manufacturing PET materials like used plastic bottles and polyester textiles. As a substitute for virgin polyester, RPSF minimizes the pollution arising from plastic waste without sacrificing demand for versatile synthetic fibres.
Key Benefits of RPSF:
-
Eco Friendly: Reduces landfill waste and ocean pollution.
-
Energy Saving: The energy required to produce RPSF is lesser than producing virgin polyester.
-
Durable and Versatile: Retains the same characteristics as virgin polyester for numerous applications.
1. Raw Material Collection and Sorting
First and foremost is the sourcing and sorting of the raw materials for RPSF production.
Sources of Raw Materials:
PET Bottles: These are generally collected from households, industries, and even landfills.
Sorting Techniques:
-
Manual Sorting: Sorting out contaminants such as caps, labels, and other non-PET materials.
-
Advanced Sorting Technologies: Higher precision done by the use of optical sensors and AI-driven systems for accuracy.
It will help the manufacturer to get better quality fibre since the PET materials have purity.
2. Cleaning and Preparation of PET Flakes
The sorted PET waste undergoes cleaning and preparation for further processing.
Steps Involved:
-
Crushing: PET bottles are crushed into small flakes using industrial crushers.
-
Washing: Flakes are washed with hot water and detergents to remove dirt, adhesives, and oils.
-
Drying and Crystallization: Flakes will be dried and set under a process of crystallization for enhancement of thermal stability.
This ensures that the PET flakes are free from contaminants and clean for extrusion.
3. Extrusion and Spinning Processes
The stage involves processing PET flakes into continuous filaments.
-
Melting: When the flakes enter the extruders, they are heated and melted into a uniform polymer.
-
Filtration: The molten polymer is passed through filters to remove impurities.
-
Spinning: Filtrated melt is forced through spinnerets, yielding long, continuous filaments.
Extrusion and spinning have direct impacts on the strength and texture of the resulting fibre.
4. Fibre Drawing and Crimping
The filaments produced during spinning are subjected to further mechanical processing.
-
Drawing: When the filaments are stretched, polymer chains arranged in a linear fashion become stronger and more elastic.
-
Crimping: Bulk and texture along with the wavy structure are given to the fibers.
-
Crimping: It is done to improve the good blending properties of the fibre in textiles
-
Heat Setting: Stabilization of Properties of Fibres, which are now stable, durable, and ready to be cut into staple fibres.
5. Staple Fibre Cutting and Finishing
The continuous filaments are cut for producing staple fibres.
-
Cutting Processing: The particular length in the range of 25 mm to 75 mm is cut depending on the application to the filaments.
-
Finishing: Finishes applied could be anti-static coatings or flame retardants. Finishes improve the fibre performance for specific uses.
-
Quality Control: Severe testing ensures the fibres match the industry standards for strength, elasticity, and uniformity.
Applications of RPSF
Recycled Polyester Staple Fibre is widely used in a range of applications owing to its versatility and durability.
-
Textile Industry: RPSF finds large applications in the manufacturing of spun yarn for fabrics, clothing, and other home textiles. It is an eco-friendly alternative to virgin polyester, thereby it offers an ideal choice for sustainable fashion.
-
Nonwoven Fabrics: RPSF is used in large volumes in nonwoven applications such as hygiene products (diapers, sanitary napkins), medical fabrics (masks, gowns), and industrial products such as filters, geotextiles.
-
Automotive Industry: The automotive industry utilizes RPSF for the manufacturing of components, which include seat fillings, carpets, and insulation materials, thus leading to lightweight, durable, and low-cost options.
-
Home Furnishings: RPSF is used in bedding which incorporates pillows, mattresses, and quilts. Besides providing comfort and support, it contributes to an eco-friendly lifestyle.
-
Insulation Materials: The fiber is used for thermal and acoustic insulation in buildings and other applications, providing an energy-efficient solution for construction and automotive industries.
-
Geotextiles: RPSF, therefore is an important manufacturing input for the production of geotextiles that are used in various processes such as in road making, erosion control, landscaping among other applications. Such applications help stabilize soil and enhance infrastructural developments.
-
Pet Products: RPSF helps in producing pet bedding and other related items by offering soft comfortable material that is derived from recycled plastics.
Environmental Footprint and Sustainability
RPSF helps reduce the carbon footprint of the textile and plastic industries.
Environmental Benefits:
-
Waste Reduction: Saves million tons of plastic waste from landfills and oceans
-
Energy Saving: This generally consumes less amount of energy compared to virgin polyester
-
Bubbles into the Circular Economy: Relies on recycling and reduces dependence on fossil fuels
Enhancements in RPSF Technology
RPSF innovations advance the industry every day
-
Chemical Recycling: PET breaks down to its monomers in order to create fibers of better quality
-
Automation: Smart AI-based sorting and processing systems
-
Eco-friendly Dyes: RPSF embraces environmentally friendly color systems
Success Cases of RPSF Companies
Leaders in RPSF manufacturing companies have established strong standards in the industry.
-
Saheb Fibre: With highly advanced recycling capabilities and of high-quality RPSF
-
Global Textile Brands: Many large international brands have begun utilizing RPSF to meet sustainability targets.
Consumer Awareness and Market Trends
Increasing consumer concern for sustainable items has boosted the RPSF market.
Market Trends:
-
More demand for environmentally friendly textiles
-
Brands that commit to sourcing from fair and environmentally friendly vendors.
Awareness Initiatives:
-
Educating the consumer about RPSF
-
Call for Transparency in the supply chain
Conclusion
The production of Recycled Polyester Staple Fibre (RPSF) is an excellent example of how recycling technologies overcome environmental troubles. On one hand, RPSF cuts down on waste and saves energy besides being sustainable. In view of this, it forms an essential development towards a greener industry. The days therefore seem bright for RPSF with developments in quality and production efficiencies.