Colored RPSF (Recycled Polyester Staple Fibre)
Leading Manufacturer and supplier of Colored Recycled Polyester Staple Fibre (RPSF), Saheb Fibre offers the textile industry a special fusion of innovation and sustainability. After being cleaned, melted, and extruded into fibres, PET bottles are carefully dyed using advanced methods to provide vivid, uniform shades that meet customer specifications.
Saheb Fibre's Colored RPSF, which is well-known for its vivid colour spectrum, is perfect for a number of uses, such as the manufacture of textiles, nonwoven materials, and upholstery for automobiles. The utilisation of recycled fibres promotes ecological practices, and the rich colour scheme improves the textile items' visual attractiveness. Saheb Fibre's Colored RPSF offers outstanding quality, durability, and environmental responsibility whether it is used for industrial, home textile, or fashion items.
The finished products' visual appeal is improved by the rich color scheme, which also gives manufacturers and designers more creative freedom. A circular economy is also supported and landfill waste is decreased as a result of Saheb Fibre's dedication to sustainable methods.
Our Product Quality Parameter
Quality Parameters | Observation | Observation | Observation | Observation | ||
---|---|---|---|---|---|---|
Sr. No. | Particular | Unit | ||||
Pearl White | Bright (Optical) White | Cotton White | Dark Black | |||
1.4 D | 1.4 D | 1.4 D | 1.4 D | |||
1 | Tenacity | GPD | >6.35 | >6.35 | >6.35 | >6.25 |
2 | Elongation | % | 18.0~22.0 | 18.0~22.0 | 18.0~22.0 | 18.0~22.0 |
3 | OPU | % | 0.180~0.20 | 0.180~0.20 | 0.180~0.20 | 0.180~0.20 |
4 | Fuse Fibre | % | <0.01 | <0.01 | <0.01 | <0.01 |
5 | Long Fibre | % | <0.0008 | <0.0008 | <0.0008 | <0.0008 |
6 | Moisture | % | <0.7 | <0.7 | <0.7 | <0.7 |
7 | Actual Denier Range | ±0.05 | ±0.05 | ±0.05 | ±0.05 | |
8 | Available Denier | % | 1.0/1.2/1.4 | 1.0/1.2/1.4 | 1.0/1.2/1.4 | 1.0/1.2/1.4 |
9 | Bale Weight | % | 350~400 | 350~400 | 350~400 | 350~400 |
10 | Max Loading Per Container | % | 28 | 28 | 28 | 28 |
Procedure of Manufacturing Colored RPSF
Colored Recycled Polyester Staple Fibre (RPSF) is a sustainable substitute for traditional colored fibres that was created to satisfy contemporary sustainability standards. Colored RPSF removes the need for water-intensive post-dyeing techniques by integrating pigments into the fibre production process using technologies like spun-dyeing. As a result, even after many washings or uses, the fibres remain brilliant, strong, and unfading. Perfect for textile, automotive, and home furnishings applications, colored RPSF is notable for its cost-effectiveness and superior colour constancy as well as its environmental advantages, which include less water use, less energy use, and fewer carbon emissions.
Dyeing Process of Colored RPSF
- Polymer Preparation: To make a uniform polymer solution, recycled polyester is cleaned and melted. By removing contaminants from the base material, this procedure improves pigment incorporation.
- Addition of Pigment: The molten polymer is immediately mixed with premium colour pigments. To guarantee even dispersion and a consistent colour throughout the fibre, the pigments are meticulously metered.
- Fibre Extrusion: To create continuous strands of colored fibres, the pigmented polymer is extruded through spinnerets. Unlike traditional procedures, which use chemicals and water to colour fibres after production, these fibres are naturally dyed because the pigments are integrated into the polymer matrix.
- Cooling and Solidification: A cooling system cools the extruded fibres, causing them to solidify into the structure and shape that are required.
- Fibre Alignment and Strengthening: To increase the strength, flexibility, and homogeneity of the polymer chains, the fibres are meticulously stretched (drawn). A gorgeously even finish is produced by this phase, which also guarantees that the colour remains constant throughout.
- Final Processing: After colouring, the RPSF is cut into staple lengths, put through a rigorous quality inspection, and packed so that it may be utilised in a range of goods, including industrial applications, textiles, and home furnishings.
Key Difference from Traditional Methods
By incorporating the dye into the polymer from the start, this process is more environmentally friendly than typical polyester manufacture, which uses post-production colouring, which uses chemicals, water, and energy. It also uses less water and produces less chemical waste. This guarantees fibres with exceptional colourfastness and consistency that are vivid, long-lasting, and environmentally responsible.
Colored RPSF (Recycled Polyester Staple Fibre) Applications in Everyday Life
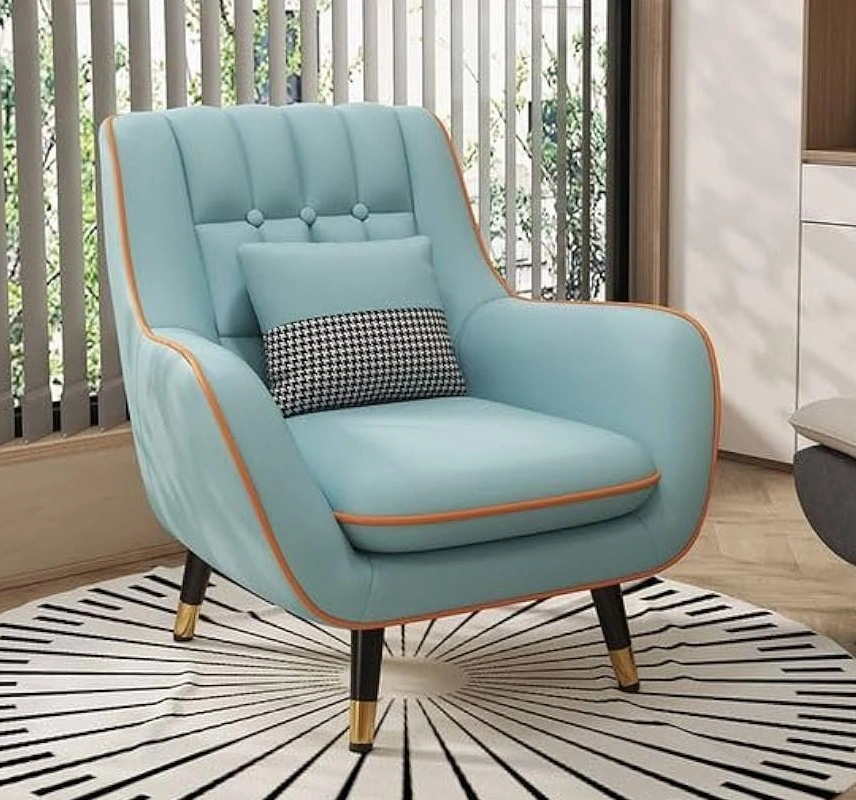
Cushioned Furniture
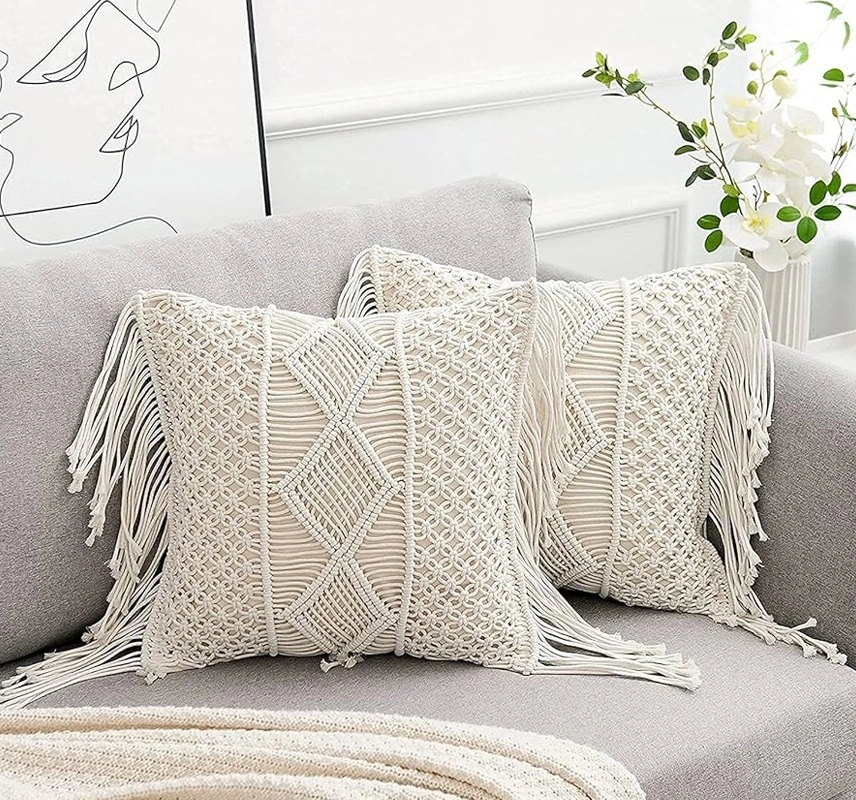
Decorative Cushions and Pillows
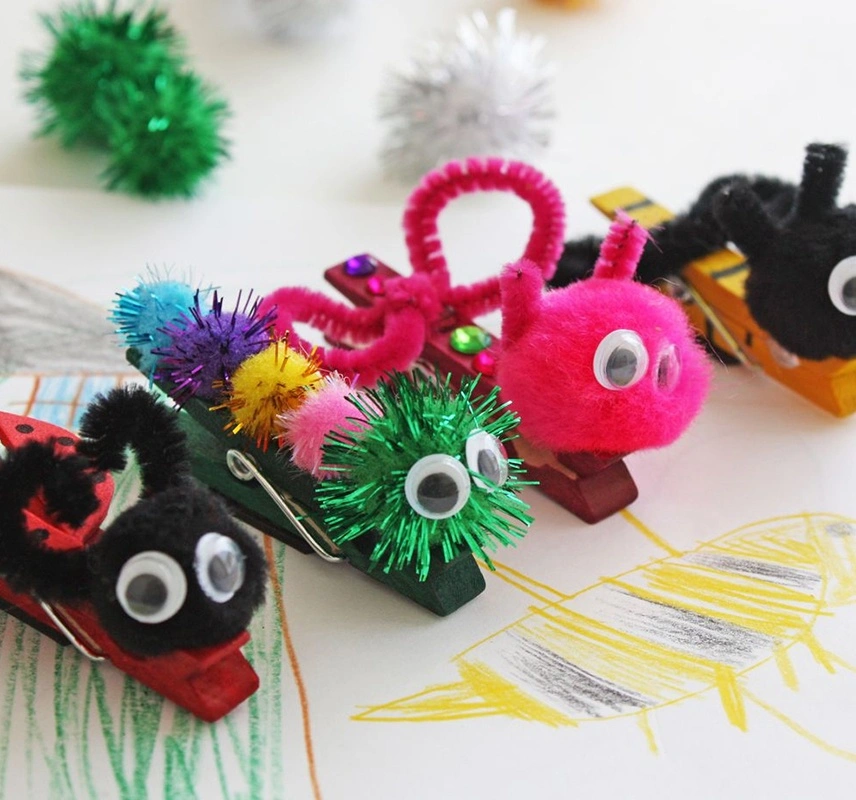
DIY Projects
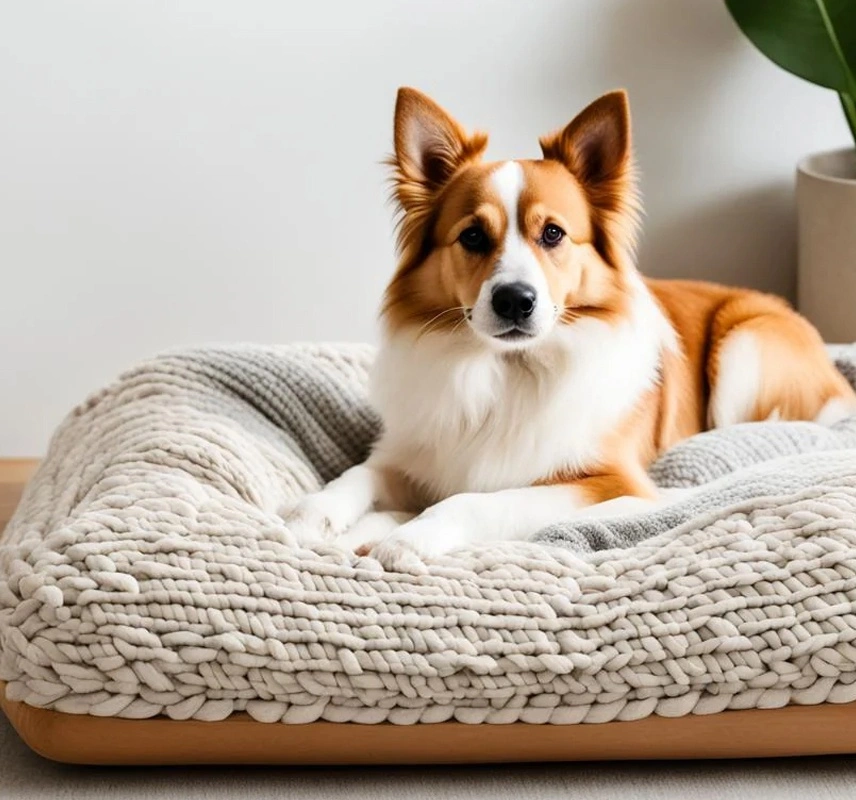
Pet Beds and Accessories
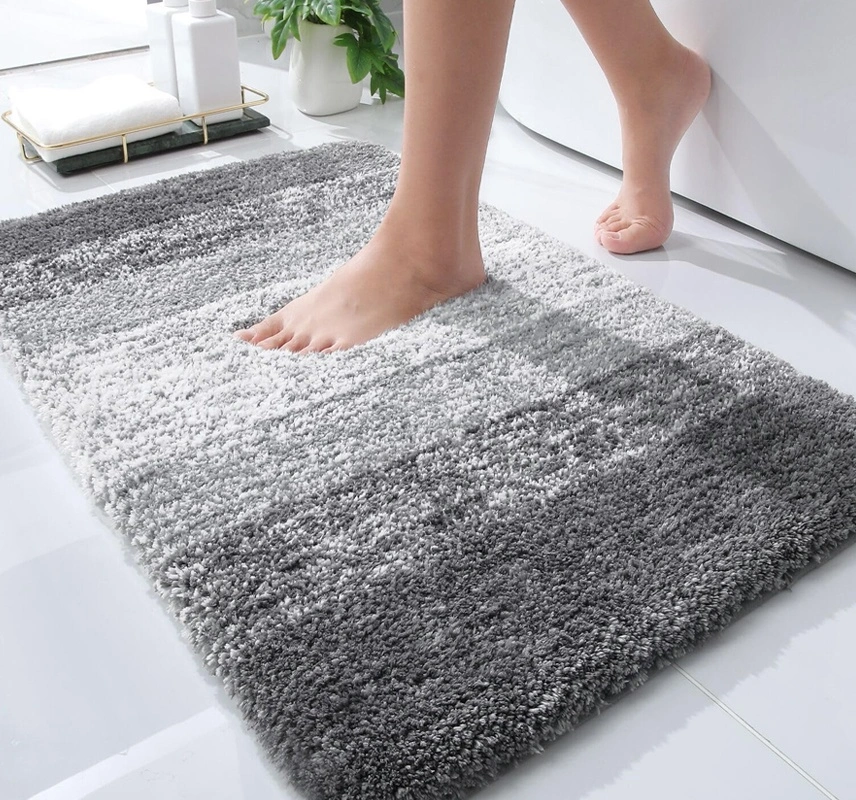
Rugs and Mats
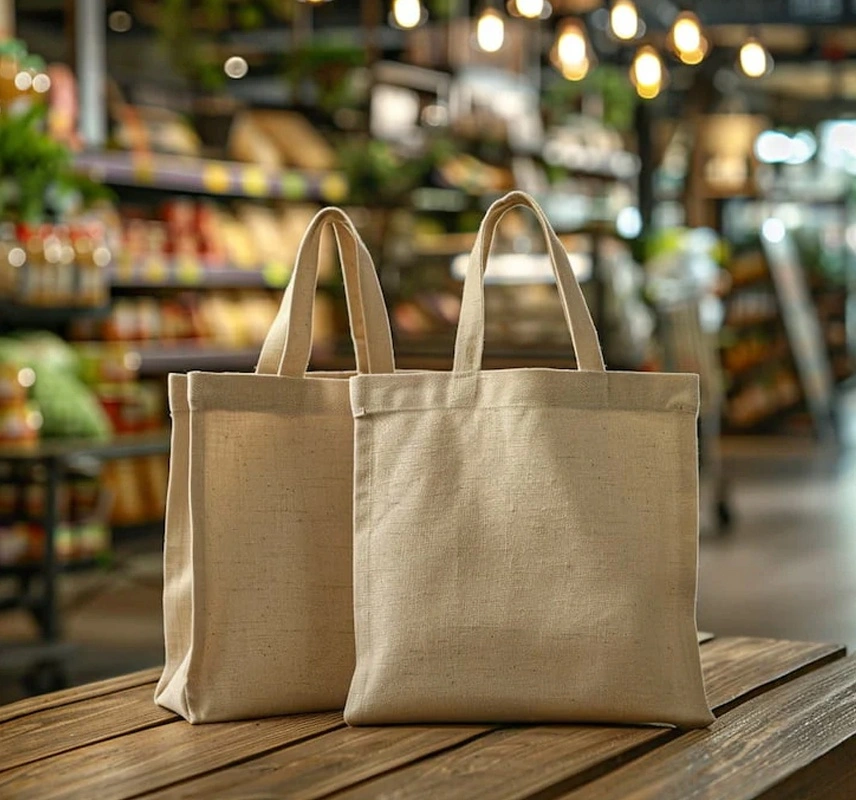
Eco-Friendly Bags
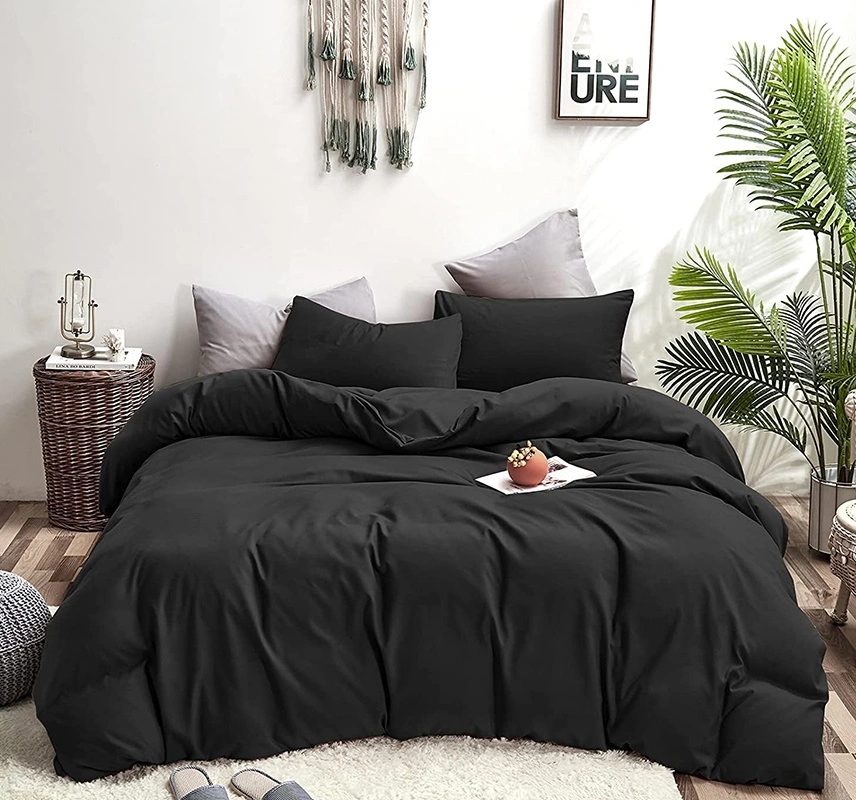
Quilts and Comforters
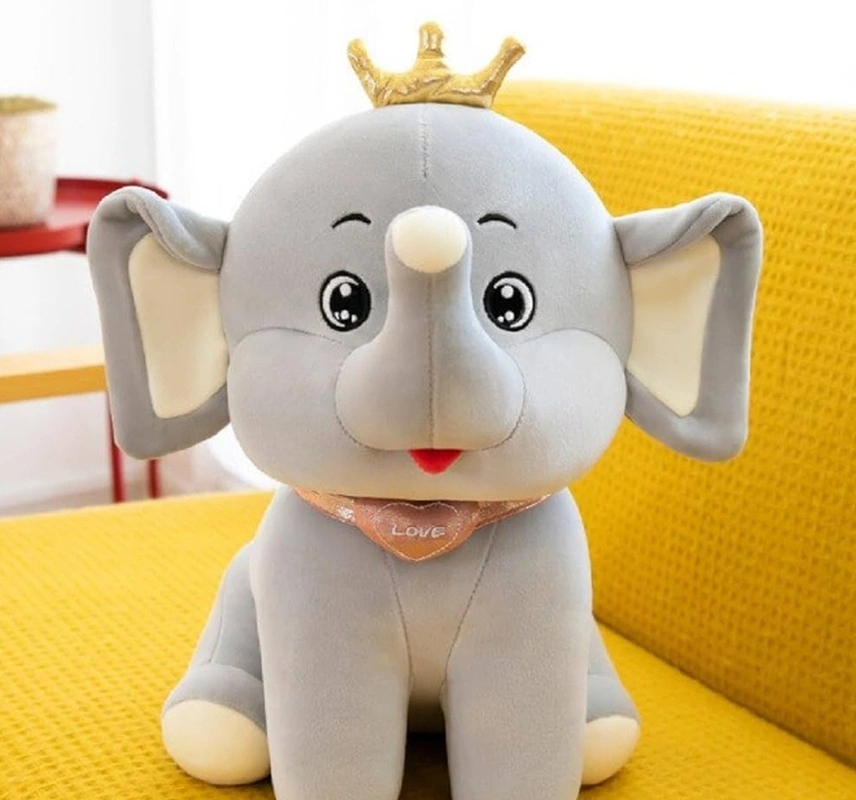